谈到飞机时,安全是至关重要的......这意味着检查。NASA的一支球队正在利用Robodk来实现多机器人检查以增加飞机的安全。
What do you think is the most important part of aircraft manufacturing? The issue of safety is probably going to be top of your list of concerns.
NASA兰利研究中心的一支团队正在使用多个机器人和Robodk来自动化和简化飞机机身的检查。
We first reported on this projecta couple of years agowhen the team started using RoboDK. At that point, they were only using one UR10 robot for an infra-red inspection system that uses short pulses of heat. At the time, they were only creating the first proof-of-concept:
“[我们想要]表明我们可以做到这项工作或比我们可以手动使用机器人系统的工作,涉及较少的劳动力。”
The project has certainly advanced in the past two years! The team is now using dual robots, combined with an external axis, and a more complex type of infra-red inspection.
Here’s how NASA uses RoboDK and why they’re now using multiple robots.
解释美国宇航局新检验任务
The inspection task that the team performs is a type of “non-destructive evaluation.” This term refers toa large group of testing processeswhich are used to detect flaws in a manufactured product without destroying the product, as the name suggests.
In particular, the team at Langley performs infra-red detection, which involves heating the fuselage and then using an infra-red camera to detect flaws in the heated material.
As branch head Elliott Cramer explained:
“In conventional tomography, you heat a large area and then you inspect one area at a time. Currently, most inspections are done on a point-by-point basis. You’ll inspect a small area, you’ll move that inspection system over the surface of the system either manually or with some kind of a scanning system.”
使用双重机器人允许它们更改它们用于“线扫描断层扫描”的方法。这涉及以一致的线路移动加热元件和红外相机。
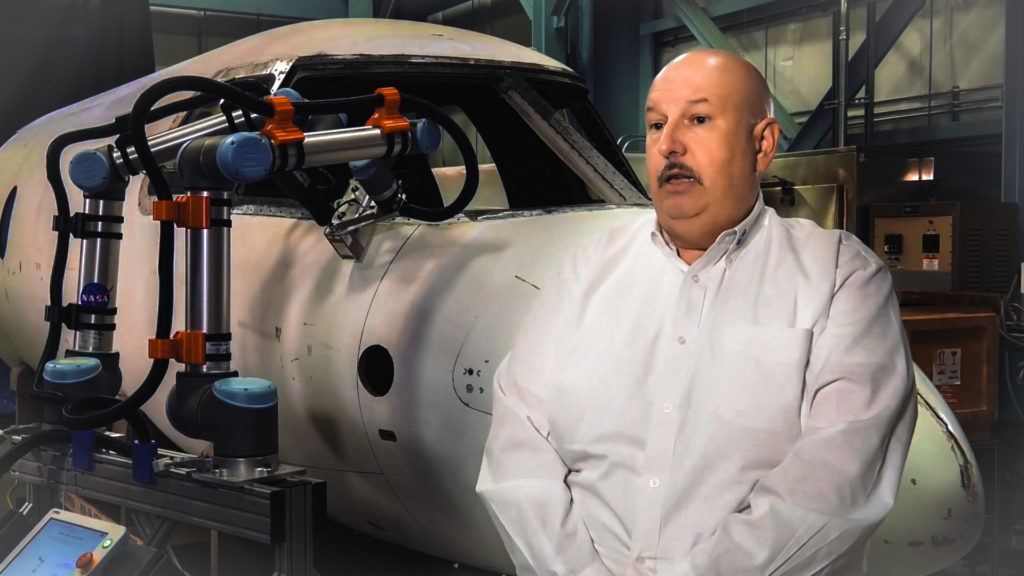
他说:
“这实际上是一种运动检查,非常适合使用机器人学。”
The Benefit of 2 Robots Over 1
When we last caught up with the project, they were using only one robot with one sensor. This new inspection method requires two robots working together collaboratively.
The two robots (bothUR10s) perform the following functions:
- The first robot holds a heating element, which it moves in a consistent line along the fuselage.
- The second robot holds aFLIR红外线相机。这沿着加热元件后面的机身沿着机身移动。捕获的图像用于形成扫描,该扫描该团队分析以检测材料中的缺陷。
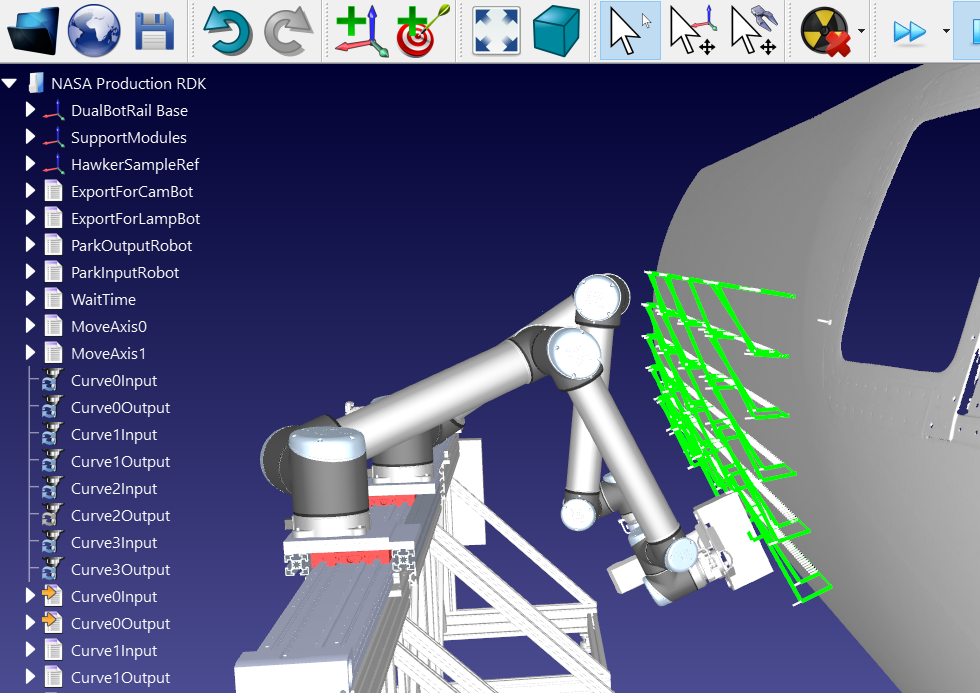
To increase the workspace of the task, the two robots are fixed onto aFesto第7轴外轴. This allows them to move along a much longer length of the fuselage and ensures that the robots move at exactly the same speed.
Why NASA Needs Robotic Inspection
与手动执行扫描相比,Elliot Cramer解释说,在这种类型的检查中使用机器人有几个好处。
Repeatability
手动扫描的主要问题之一是每次都不能将传感器定位在完全相同的位置。用手重新定位传感器以仔细检查阅读将永远采取。
使用机器人删除此问题。
克莱默解释:
“主要优点是可重复性。如果您需要再次返回检查位置,可以重新检查或使用另一种技术。拥有机器人允许您非常准确地返回。“
速度和准确性
Another issue with manual inspection is that it takes a long time. Improving this speed was a core aim of this application:
“The goal of this project is to increase the rate of inspection and the accuracy of inspection that’s currently going on, whether that’s done in the manufacturing environment right after the fuselages have been made or if it’s done at a later time during in-service inspection of the aircraft.
“You can now cover large areas, you can handle the complex curves of the aircraft, but in a much more rapid fashion. This is designed to speed that process up but still get the same accuracy.”
Autonomy and Coverage
The team’s previous manual inspection required several technicians working together. This was quite inefficient. However, even with multiple people, it wasn’t certain that they would achieve full coverage of the aircraft fuselage due to the inaccuracies caused by manually placing the sensor.
Cramer explained that both of these problems have been overcome by using the robotic system:
“It can autonomously go off and do the inspection once it’s been programmed and we are ensuring 100% coverage.”
NASA如何使用ROBODK
Robodk在NASA的检查应用中播放了一个关键部分。将多个机器人与RoboDk组合并将外部轴结合到编程中很容易。
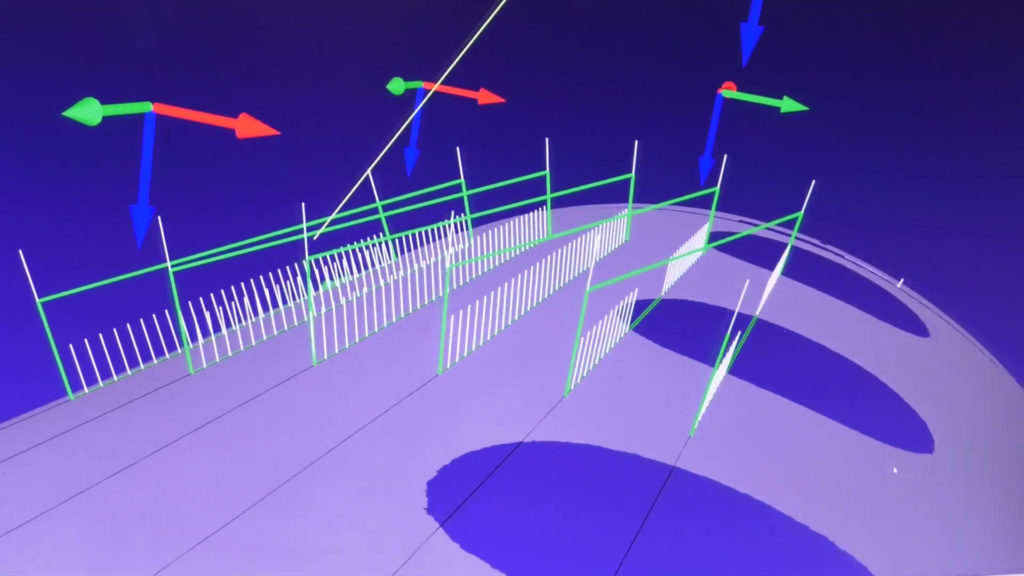
Here’s the process that they use for the inspection:
- 与A.Creaform光学扫描仪,工程师首先创建机身的表面图。这是手动进行的。
- 使用扫描数据,它们能够准确地定位空间和相对于机器人的机身。
- 它们在Robodk中创建了路径,它自动生成机器人代码。
- 机器人执行检验任务并构建机身的红外扫描。
- Using马铃薯草,工程师然后分析扫描缺陷。
As you can see, this is a perfect example of a multi-software workflow, whichRobodk旨在促进.
项目的下一步是什么?
The team has achieved an impressive improvement of their inspection process using multi-robots and RoboDK.
But, they have further plans for the application.
艾略特克莱默解释说:
“One of the other things that we’re working towards is the ability to automatically map the data that we collect to an image of the fuselage. That will ensure the long term durability of those vehicles as they fly. And have a long-term digital record of that.
“最终目标是提高航空旅行的安全。“
Which parts of your inspection processes could benefit from multiple robots?Tell us in the comments below or join the discussion onLinkedIn,推特,Facebook,Instagram.或者the RoboDK Forum.